Software as a service (SaaS)
Operational enablement through localised technology
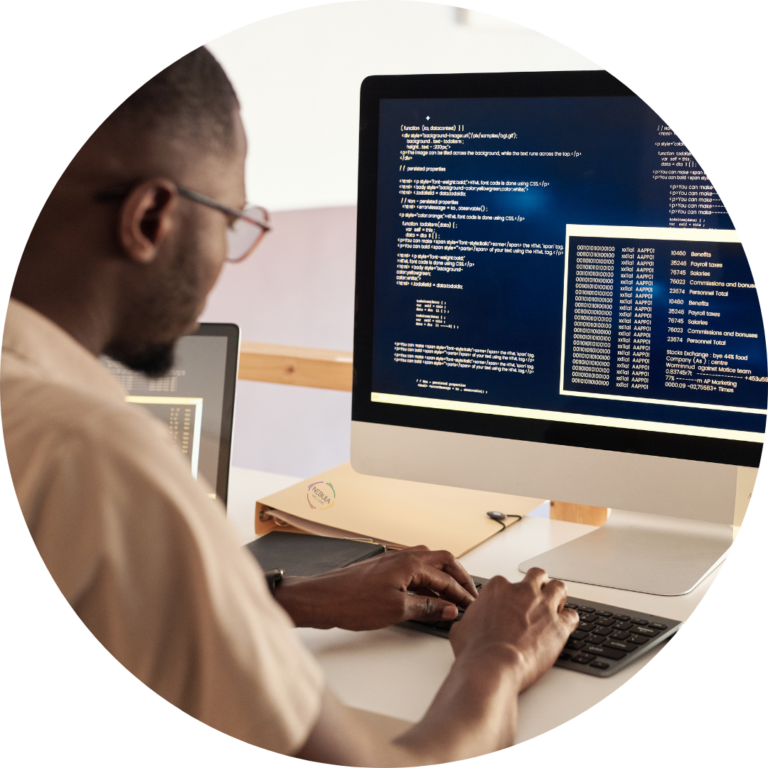
Cloud-based applications
Nebula is a proud partner and endorser of the AdOr warehouse management system (WMS) and Ramco transport management system (TMS) technology platforms
Warehouse management system (WMS)
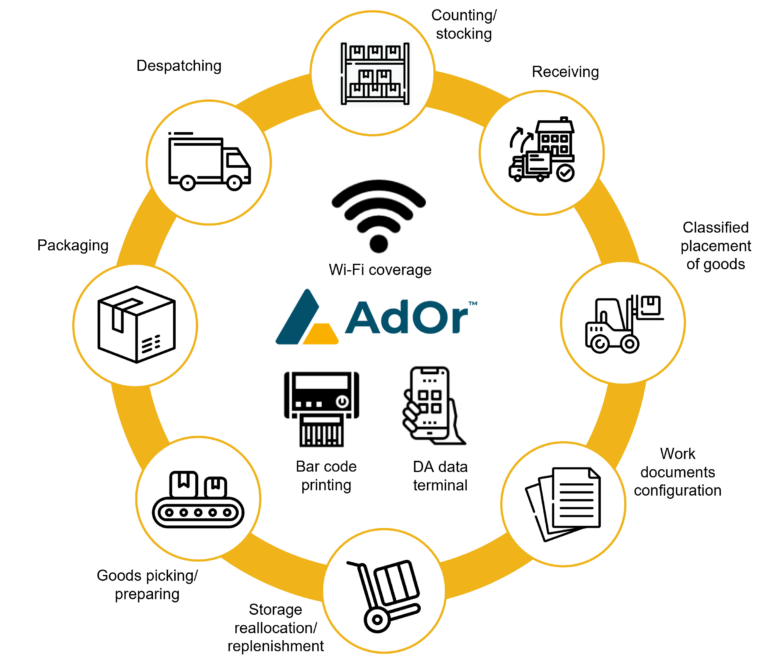
WMS high-level process
Agile and flexible AdOr WMS software
WMS core capabilities
Receiving
Accepting and processing incoming goods in a warehouse. This includes unloading, inspecting, and entering items into the WMS.
Inspection/quality assurance
Inspecting incoming goods to ensure they meet specified standards and are free from defects. This step helps maintain inventory accuracy and product quality.
Put-away
The process of moving received goods from the receiving area to their designated storage locations within the warehouse.
Cross-docking
A logistics strategy where incoming goods are directly transferred to outbound vehicles with minimal or no storage time, speeding up delivery and reducing storage costs.
Location management
Assigning specific locations to items within a warehouse to optimise storage and retrieval processes.
Inventory management
Tracking and managing inventory levels, orders, sales, and deliveries to ensure the right amount of stock is available at the right time.
Replenishment
Moving inventory from reserve storage to picking locations to ensure that items are available for order fulfilment.
Picking
Retrieving items from their storage locations to fulfil customer orders.
Wave management
Grouping orders into batches or “waves” for processing based on specific criteria such as shipping schedules or order priorities.
Staging
Temporarily holding goods in a designated area before they are moved to their final destination, such as the shipping dock.
Packing
Preparing items for shipment, including boxing, labelling, and ensuring the correct items are included in each order.
Truck loading
Loading packed goods onto trucks for transportation to their final destination.
Manifesting
Creating a detailed list of the contents of a shipment, including item descriptions, quantities, and other relevant information.
Cycle counting
A method of inventory auditing where a small subset of inventory is counted on a regular basis to ensure accuracy.
Extended WMS capabilities
Labour management
Managing and optimising the workforce within a warehouse, including scheduling, task assignments, and performance tracking.
Yard management
Managing the movement and storage of trailers and containers in the yard area of a warehouse or distribution centre for inbound deliveries, as well as outbound loads.
Slotting
Organising and assigning products to specific locations within a warehouse to optimise picking efficiency, can be a system-driven rule-based process.
Third-party billing
Managing billing and invoicing for services provided by third-party logistics providers.
Task interleaving
Combining multiple tasks into a single trip to increase efficiency, such as picking and replenishment.
Dock scheduling
Planning and managing the arrival and departure times of trucks at the loading docks to optimise the flow of goods.
Value-added services
Additional services provided in the warehouse, such as kitting, labelling, or assembly, that add value to the products.
Parcel management
Managing the shipping and tracking of small packages and parcels.
Think our WMS can work for you?
Transport management system (TMS)
TMS process lifecycle overview
Our advanced TMS is designed to streamline operations and enhance efficiency
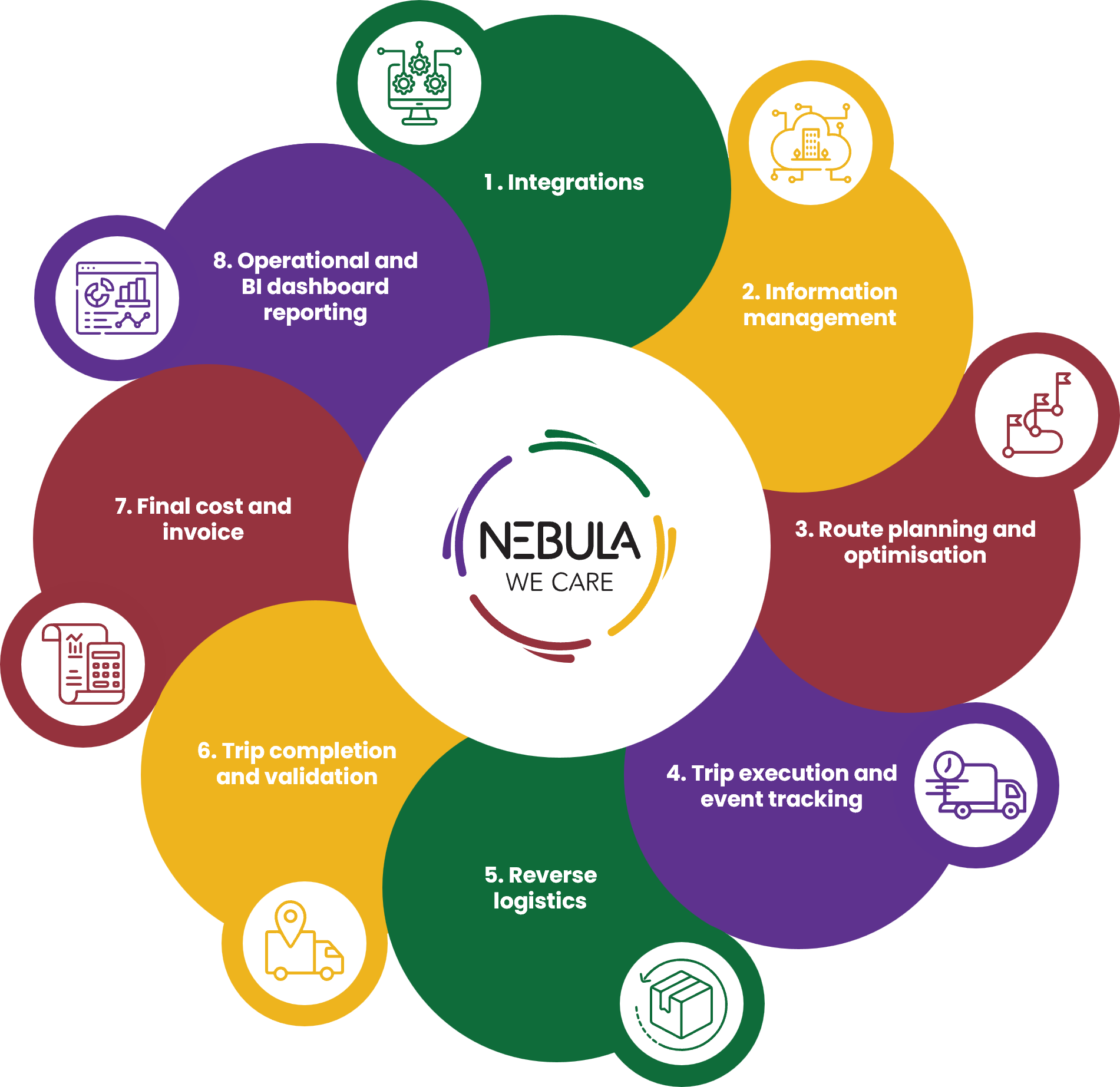
1. Integrations
Enables seamless data exchange between the TMS and other systems (ERP, WMS), enhancing operational efficiency and reducing manual data entry.
2. Information management
Ensures accurate master data and validates business rules, providing reliable information that drives informed decision-making and compliance
3. Route planning and optimisation
Automatically generates cost-effective delivery routes, reducing transit times and transportation costs while maximising resource utilisation.
4. Trip execution and event tracking
Facilitates real-time despatching and communication with drivers, ensuring timely deliveries and the quick resolution of any issues that arise. Provides real-time visibility into shipment status, keeping all stakeholders informed allowing for the proactive management of delivery processes.
5. Reverse logistics
Streamlines the return process for products, minimising costs and enhancing customer satisfaction through the efficient handling of returns and exchanges.
6. Trip completion and validation
Confirms successful deliveries and captures the necessary documentation, ensuring accountability and accuracy in the logistics process.
7. Final cost and invoice
Automates invoicing based on accurate data, improving cash flow management and reducing disputes through transparent billing practices.
8. Operational and BI dashboard reporting
Offers insights through visual dashboards, enabling performance analysis and data-driven decisions that enhance the overall supply chain efficiency.
TMS capability that creates value
Transform your logistics with our advanced TMS, designed to streamline operations and enhance efficiency. Our TMS solution offers real-time visibility, optimised route planning and automated processes, reducing operational costs and increasing on-time deliveries. With seamless integration into your supply chain, our TMS enhances decision-making, improves customer satisfaction and ensures regulatory compliance. Experience reduced transportation spend, improved resource utilisation and the agility to adapt to market changes. Elevate your business with a smarter, faster and more efficient TMS solution tailored for growth.
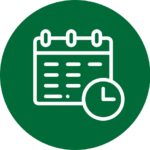
Optimised planning
Automate your planning process based on business-specific rules to ensure on-time delivery and reduce service costs, enhancing efficiency and customer satisfaction.
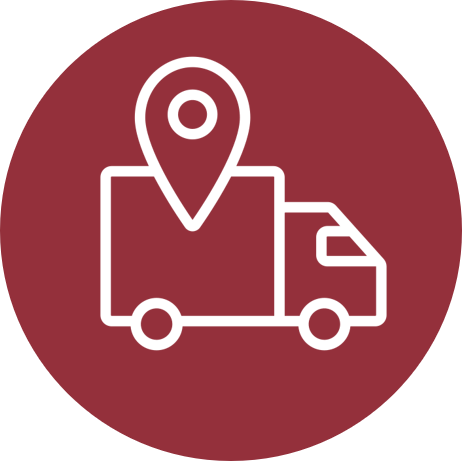
Real-time visibility
Gain complete end-to-end shipment tracking to monitor delivery status, proactively address issues and elevate customer service with real-time insights.
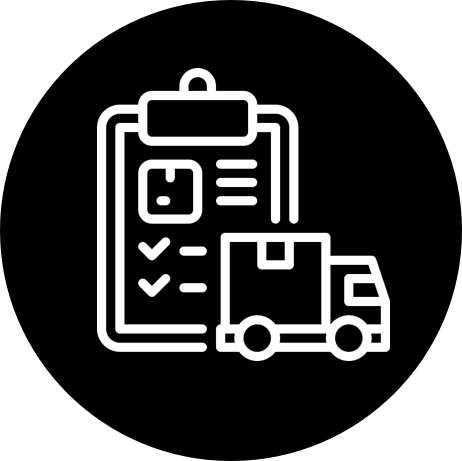
Carrier selection and freight rating
Automatically select carriers based on rates, performance and capacity, ensuring cost-effective transportation without compromising service levels.
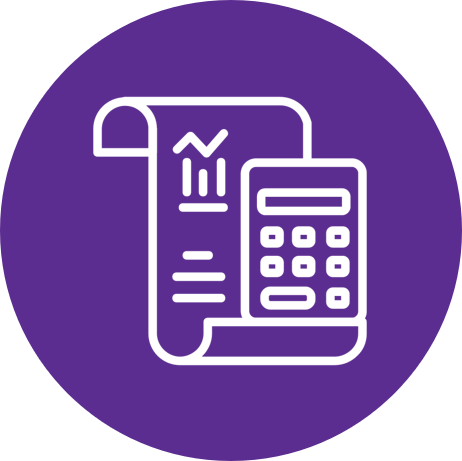
Contract management with rating and billing
Control transportation costs while maintaining service quality. Ensure transparent rate management and streamline the cash-to-cash cycle with integrated final-cost invoicing.
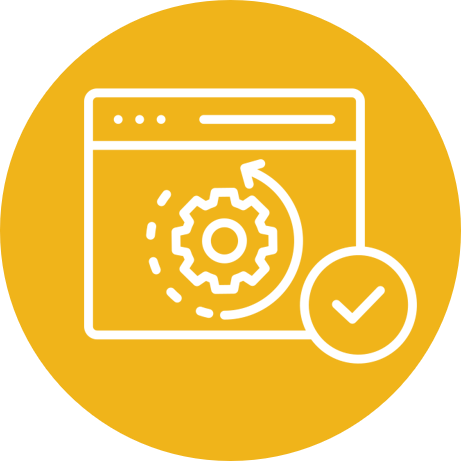
Automated documentation
Streamline operations by automating critical shipping documents such as bills of lading and invoices, reducing errors and improving processing speed.
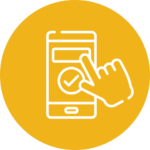
Driver mobile application
Execute deliveries seamlessly with live event tracking, customer signature capturing and electronic proof of delivery (ePOD), ensuring smooth invoicing and client satisfaction.
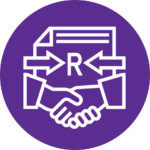
Tender management
Optimise procurement for high-volume lanes with spot-bid tendering to secure the best available rates.

Hub and cross-dock management
Plan and manage inbound and outbound shipments with a cross-dock module, efficiently handling unit management from parent to child.
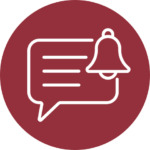
Event notifications and alerts
Configure alerts to send real-time mobile or email notifications throughout the delivery cycle, keeping stakeholders informed of critical milestones.
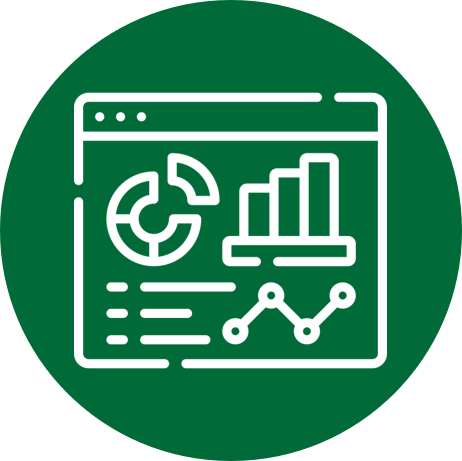
Business intelligence dashboards
Leverage performance dashboards to track and improve supply chain performance, driving actionable insights for operational excellence.